6 A Brief History of 3D Printing
3D printing is the process of layering or printing material bit by bit to create an item. When I explain 3D printing to people who are new to the concept, I ask them to imagine using a glue gun to pile layer upon layer until an object is formed.
3D printing, while now a fairly mainstream term, is still a new and evolving technology that is changing the way we prototype and manufacture. Additive manufacturing, another term for 3D printing, has a surprisingly long history dating as far back as the 1980s.
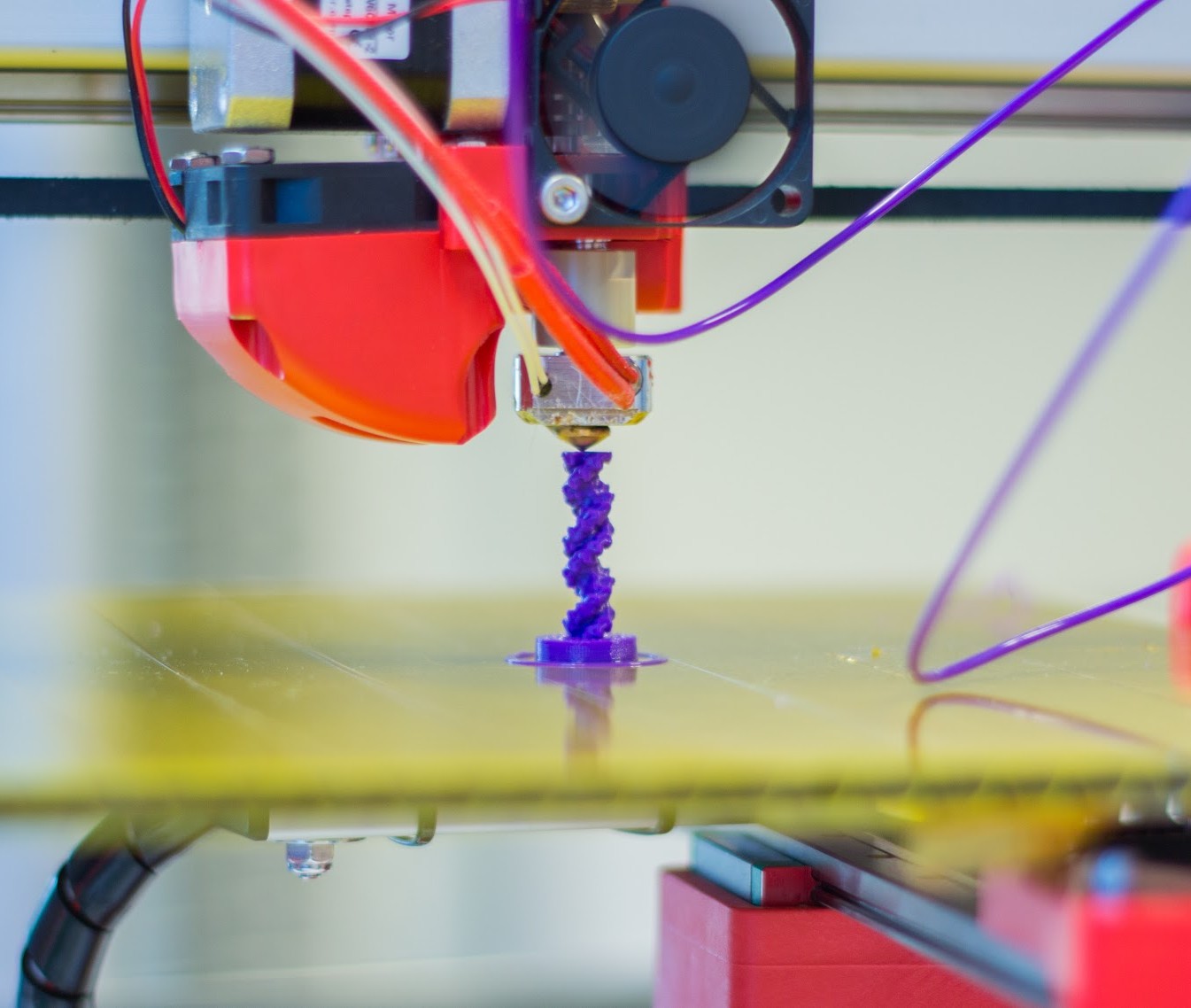
Early Development
In the 1980s the first ever 3D printer was patented by Chuck Hull. It used a technique which he called stereolithography (SLA) which is still in use today. The printer functioned by curing, or hardening, successive layers of photosensitive resin one on top of another to gradually build up an object. Hull’s printer was defined in his 1986 patent as an “Apparatus for Production of Three-Dimensional Objects by Stereolithography.”
A similar patent application had been submitted a few weeks ahead of Hull’s by a team of French inventors led by Alain Le Mehaute. Surprisingly, their patent application was ultimately abandoned because a long-term viable use for the technology could not be identified.
Other methods of additive manufacturing being explored and developed in the 1980s included Selective Laster Sintering (SLS) invented by Carl Deckard, Direct Metal Laser Sintering (DMLS) from German Company EOS GmbH, and Fused Deposition Modelling (FDM) by S. Scott Crump. Stratasys, the company which Crump later co-founded with his wife Lisa, has remained a leading producer of FDM printers.
Early 3D printers were far beyond the price point of every day consumers and were primarily used by large manufacturing corporations as part of their prototyping process.
Common 3D Printing Methods
Fused Deposition Modelling (FDM): FDM is the most common and affordable form of desktop 3D printing in the consumer market. A thermoplastic filament is heated and gradually deposited through a nozzle onto a build-plate in x and y coordinates as the object is built in a z-direction. Example: Ultimaker 3
Stereolithography (SLA): A layer of liquid photosensitive resin is exposed to a UV-laser beam. The resin hardens where the beam has struck it, and the object is built one layer at a time. After printing, the object must be washed to remove any uncured resin and then further exposed to UV light to finish curing completely. Example: FormLabs Form 3
Digital Light Processing (DLP): DLP technology is similar to SLA but differs in that it uses more conventional light sources which are controlled using micro mirrors. A liquid crystal display panel masks areas of the object which should not be exposed to light. Example: Flashforge Hunter
Selective Laser Sintering (SLS): A laser is used to solidify and bond small particles of plastic, ceramic, glass, metal or other materials layer by layer to produce a 3D object. The print bed lowers into the particles and a new layers are added one at a time. Example: Fuse 1
Selective Laser Melting (SLM): SLM is similar to SLS except that rather than compacting, or sintering, the powdered material, it is fully melted.
Electronic Beam Melting (EBM): EBM is similar to SLM. However, it uses an electron beam to melt a metal powder in place of a laser.
Laminated Object Manufacturing (LOM): Layers of material are coated with adhesive and fused using heat and pressure. They are then cut with a laser cutter.
Consumer-Grade Technology
Between 2002 and 2014 over 200 early 3D printing patents expired. The expiration of the patent on the FDM printing process opened the field for significantly more affordable consumer and hobbyist focused 3D printers to be developed.
The RepRap was one of these early low-cost 3D printers. It was made primarily from plastic parts and its creators envisaged that it could be used to print the parts for other printers. This would make it self-replicating and it would evolve as users made improvements to the design. The RepRap project is open source and as such designers are free to make changes as long as they allow their designs to be freely used by others (not unlike this open textbook).
A number of other FDM and SLA consumer-level printers quickly entered the market allowing the technology to grow, change and improve as makers learn more and share resources about the technology.